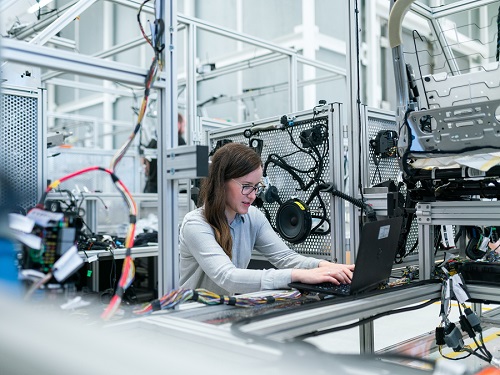
In this insight, we look at what a digital twin is, what the benefits of using one are, and which industries commonly use digital twins.
What Is It?
A digital twin is an accurate virtual model of a physical object that uses data gathered from sensors on the physical object to run simulations, study performance issues and generate possible improvements. The improvements discovered during testing of the virtual version of the object can then be made to the physical object.
Dates Back To 1960s NASA
The first use of digital twin technology dates back to NASA’s use of exact earthbound replicas of voyaging spacecraft being used for study and simulation purposes by flight crews. Fast forward a few decades and Dr Michael Grieves of the University of Michigan introduced the digital twin software concept to manufacturing in 2002.
Why Use A Digital Twin?
The reasons for using a digital twin include:
– The scale and complexity of the real object and the need to safely carry out tests without damage, disruption, and costs of having to remove/replace, get close to the object.
– Some objects may be critical to processes and/or worth enough to invest financial resources in to create a digital twin to ensure the best possible performance and add value.
– Digital twins can be used to study more issues from far more vantage points than standard simulations and have greater potential to improve products and processes.
Types of Digital Twins
Different types of digital twins include:
– Component twins/parts twins. These are used for smaller, individual component parts.
– Asset twins. These are used to study how the interaction between two or more components (known as ‘asset’) could be improved.
– System/unit twins. These are used to help improve performance by studying how assets work together in a system.
– Process twins. This is larger-scale digital twin, used to improve the effectiveness of whole systems such as an entire production facility.
Which Industries Use Digital Twins?
Examples of industries that typically use digital twins include:
– Construction (and engineering) – e.g., for buildings, bridges, and other complex structures.
– The Aerospace and automotive industries – e.g., creating digital twins for parts of turbines, automobiles, and aircraft. Also, the use of digital twins may be vital to improving the performance and safety of EV batteries, thereby helping to push the EV market forward.
– Manufacturing – to help improve efficiency, competitiveness, design customisation, predictive maintenance, shop floor matters and product development.
– Energy/power – e.g., using digital twins to help improve mechanisms for generating power and transmitting it.
– Healthcare – e.g., to improve personalised care.
– Supply chain – e.g., Optimizing warehouse design and operational performance and creating a logistics network.
– Retail – e.g., customer modelling and simulations.
The Benefits of Digital Twins
The benefits of digital twins include:
– Saving costs, time, and generating competitive advantage in production by enabling more effective research and design of products, thanks to the large amount of data that can be created about performance outcomes.
– Enabling streamlining and peak efficiency to be maintained due to being able to constantly monitor and test the digital twin.
– Better product decision-making by helping manufacturers to decide what should happen to products at the end of their lifecycle – i.e., matters relating to final processing, recycling, and choosing which product materials to be harvested.
Challenges To Digital Twin Technology
Some of the main challenges to digital twin technology include:
– Possible security issues – i.e., potential theft/compromising of the large amounts of data generated and flowing between multiple devices.
– Management of sometimes complex system of design data for digital twins perhaps amongst partners and suppliers.
– The cost and complexity may be an issue for smaller companies, thereby possibly putting them at a disadvantage to larger competitors.
What Does This Mean For Your Business?
Digital twin technology provides a way for businesses and organisations to gain new insights into their products, processes and systems that can drive improvements in efficiency and help to create value and innovation. Having a virtual copy that works on data from the real object offers more vantage points than standard simulations and gives businesses the opportunity to gain a much better understanding of products and systems while saving them time and money.