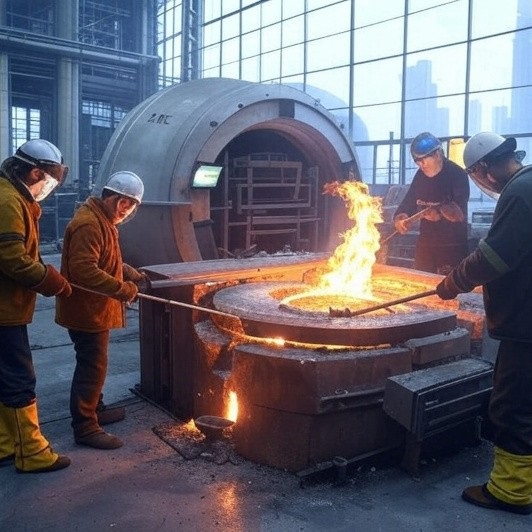
In a UK-first, researchers have achieved a significant milestone in the journey towards sustainable energy by producing fusion-ready steel on an industrial scale.
NEURONE Producing RAFM
In a UK-first, the NEURONE (Neutron Irradiation of Advanced Steels) consortium, led by the UK Atomic Energy Authority (UKAEA), has successfully forged 5.5 tonnes of reduced-activation ferritic-martensitic (RAFM) steel. This material is uniquely capable of withstanding the intense heat and neutron radiation inside a fusion reactor, laying the groundwork for cost-effective manufacturing of fusion-grade materials. This groundbreaking achievement not only holds the promise of reducing the costs of nuclear fusion but also addresses key challenges in the development of this cleaner, virtually limitless energy source.
The Challenge of Fusion Energy Materials
Nuclear fusion, the process that powers the Sun, is thought to be the ultimate solution to the world’s energy crisis. Unlike nuclear fission (from current nuclear reactors), fusion produces no long-lived radioactive waste and relies on fuels like deuterium, which can be extracted from seawater, and tritium, which can be bred from lithium, both of which are abundantly available. Fusion, therefore, has the potential to provide virtually limitless energy without greenhouse gas emissions, addressing the twin challenges of energy security and climate change.
Fusion’s promise comes at a time when the world urgently needs scalable, clean energy alternatives to fossil fuels. Unlike solar or wind, fusion could deliver consistent, base-load power without dependence on weather conditions. However, achieving this vision is no small feat. Inside a fusion reactor, hydrogen atoms are superheated to temperatures over 150 million degrees Celsius to form plasma, which must be contained and stabilised to sustain the reaction.
It’s Not So Much The Heat, It’s The Neutron Radiation Damage
Materials play a critical role in this process, as reactor walls must be able to withstand the extreme environment created by fusion reaction. Neutron radiation from the fusion process is particularly damaging, degrading materials over time. As explained by Ryan Ramsey, Chief Operating Officer at British fusion startup First Light Fusion, “The biggest problem isn’t the heat, it’s neutron damage.” Without materials like reduced-activation ferritic-martensitic (RAFM) steel, capable of enduring both intense heat and neutron loads, reactors would face frequent repairs, undermining their efficiency and commercial viability.
The Breakthrough By UK Researchers
The NEURONE team, working in collaboration with the Materials Processing Institute (MPI) in Middlesbrough, used a seven-tonne electric arc furnace (EAF) to produce RAFM steel at an industrial scale. Previously, the production of such steel was limited to laboratory-scale quantities. This technological leap is set to reduce production costs by up to 90 per cent, thanks to the scalability and efficiency of EAF technology.
“This is a groundbreaking moment for nuclear fusion R&D,” says Richard Birley, NEURONE project lead at MPI. “As the only sovereign UK steel research facility able to produce RAFM steel at this scale, we are proud to contribute to a future powered by sustainable fusion energy.”
Fast Workers
The project’s achievements were surprisingly swift. For example, within its first year, NEURONE was able to produce a substantial 5.5 tonnes of fusion-grade steel. The programme has also developed over 50 variants of advanced RAFM steel, designed for analysis and optimisation, ranging from small-scale melts of 100 grams to full industrial batches.
Why It Matters for Sustainability
This breakthrough could have far-reaching implications for the future of fusion energy and sustainability. Fusion powerplants, for example, could offer a virtually limitless source of clean energy with no greenhouse gas emissions and minimal long-lived radioactive waste. However, building commercially viable reactors hinges on solving technical challenges like material durability and cost efficiency.
On the UKAEA website, David Bowden, NEURONE programme lead and Group Team Leader for Materials Science and Engineering at UKAEA, highlights the importance of this achievement, saying: “One of the major challenges for delivering fusion energy is developing structural materials able to withstand the extreme temperatures and high neutron loads required by future fusion powerplants.”
The new steel’s ability to withstand temperatures up to 650°C is particularly significant. Higher operational temperatures mean more heat can be extracted from the fusion reactor, improving overall energy efficiency. As Bowden puts it, “Developing these types of steel could also benefit adjacent industries that require high-strength, high-temperature structural steels, such as nuclear fission or petrochemicals.”
Economic and Environmental Impact
With this latest breakthrough, the electric arc furnace used by MPI operates on electricity rather than coal, thereby aligning with broader goals to decarbonise industrial processes. By leveraging existing supply chain infrastructure, NEURONE’s approach could make fusion steel production not only cheaper but also more environmentally sustainable.
UK Could Now Be a Key Player in Global Transition to Clean Energy
The UK’s leadership in fusion-ready steel production may also now position it as a key player in the global transition to clean energy. Also, fusion startups, such as Oxford-based First Light Fusion, stand to benefit directly from this progress. For example, as Light Fusion’s CEO Ryan Ramsey notes, “This is really positive and potentially has relevance for all fusion energy projects.”
Collaboration Driving Innovation
The NEURONE consortium’s success is rooted in collaboration. For example, supported by a £12 million investment, the project brings together academic and industrial partners from across the UK and beyond, including the Universities of Swansea, Sheffield, Birmingham, Manchester, and Oxford, as well as the Australian Nuclear Science and Technology Organisation (ANSTO).
By supporting PhD students and internships, NEURONE is also nurturing the next generation of researchers in fusion materials science. This is a vital investment in the future of both the fusion industry and the UK’s scientific leadership.
Still a Long Road Ahead
While this breakthrough is a significant step forward, fusion energy remains a challenging goal that still seems some way off. That said, the International Atomic Energy Agency optimistically estimates that commercially viable fusion powerplants could be operational by 2035. However, scaling up the production of advanced materials, like NEURONE’s RAFM steel, is essential for realising this timeline.
Looking ahead, the NEURONE team aims to refine and optimise RAFM alloys to meet even higher performance targets. As Bowden explains, “We plan to produce advanced variants of RAFM steel capable of operating at up to 650°C – a stretch target, given the solid-state physics of irradiated materials behaviour.”
What Does This Mean For Your Organisation?
This breakthrough in fusion-ready steel production could be a crucial step forward in the quest to make nuclear fusion a viable, sustainable energy source because it tackles the key challenge of developing structural materials capable of withstanding the extreme environments inside fusion reactors. The success of the NEURONE consortium demonstrates that industrial-scale production of specialised RAFM steel is actually achievable and cost-effective, thereby making fusion technology one step closer to reality. Also, the collaboration between UK industry and academic partners has not only advanced materials science but also positioned the UK as a key contributor to global fusion research.
However, while this progress is remarkable, the path to commercial fusion remains long and complex. Challenges still exist in perfecting reactor designs, scaling up materials production, and proving that fusion power can deliver electricity at a competitive price. For all its potential, fusion is not a guaranteed solution yet.
That said, the global push toward cleaner energy sources makes breakthroughs like this all the more significant. If nuclear fusion can eventually be realised, it would represent an energy revolution that’s capable of addressing climate change, ensuring energy security, and reshaping the way power is generated across the globe. Until then, every advance, such as NEURONE’s success with RAFM steel, should be celebrated because it brings that vision closer to becoming reality.