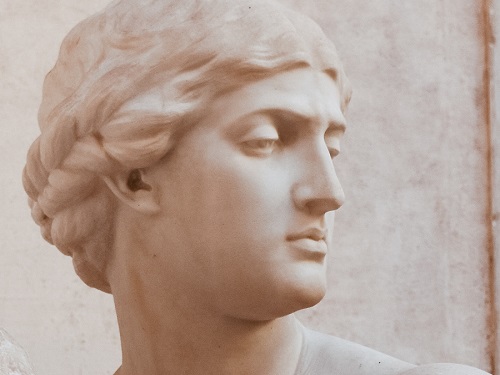
Researchers at the Swiss Federal Institute of Technology Lausanne (EPFL) have developed a way for using a 3D-printing ink that contains calcium carbonate-producing bacteria, giving a result similar to mollusc shells or bone.
‘BacktoInk’ – Environmentally Friendly
Researchers at EPFL’s Soft Materials Laboratory in the School of Engineering have successfully added the Sporosarcina pasteurii bacterium to 3D printing ink. When mixed with a urea-containing solution, it triggers a mineralisation process that produces calcium carbonate (CaCO3) that is light, strong, porous, and rigid, just bone or shells. This means that, using the new ‘BactoInk’, it’s now possible to produce a 3D-printed product of virtually any shape, using environmentally friendly materials and processes, which will gradually mineralise over the course of a few days to a solid state.
Mineral Particle Inks Failed In The Past
Inks containing mineral particles have been tried in the past but have not been able to meet the flow conditions needed for successful 3D printing i.e., behaving like a solid when at rest, but still be extrudable through a 3D printing nozzle. Also, previous efforts have resulted in structures that were soft, or shrunk upon drying, leading to cracking and loss of control over the shape of the final product.
The Answer – A Polymeric ‘Scaffold’ Using BactoInk
Lab head Esther Amstad explained why the bacteria-based ink method from the EPFL team has been successful where other mineral inks have failed, saying: “We came up with a simple trick: instead of printing minerals, we printed a polymeric scaffold using our BactoInk, which is then mineralised in a second, separate step. After about four days, the mineralisation process triggered by the bacteria in the scaffold leads to a final product with a mineral content of over 90 per cent.”
The Result – A Strong And Resilient Bio-composite
EPFL has reported that using BactoInk in a 3D printer produces a “strong and resilient bio-composite, which can be produced using a standard 3D printer and natural materials, and without the extreme temperatures often required for manufacturing ceramics.”
No Living Bacteria In Final Product
For those concerned about any possible dangers of the bacterial element of the ink, the EPFL researchers report that: “Final products no longer contain living bacteria, as they are submerged in ethanol at the end of the mineralisation process.”
What Does This Mean For Your Organisation?
This method of mineralising ink appears to have succeeded where others have failed and it’s believed that the versatility of BactoInk, combined with its low environmental impact and the excellent mechanical properties of the mineralised materials, could bring new possibilities for fabricating lightweight, load-bearing composites that are more like natural materials than to today’s synthetic composites. As such, the BactoInk method could have applications across a broad range of fields, including art, ecology, and biomedicine. The research team, for example, have suggested that it could be used in restoration of artworks e.g., by being directly injected into a mold or target site such as a crack in a vase or a chip in a statue. BactoInk’s mechanical properties such as its strength and shrinkage resistance mean that it could be well suited to both the repair a work of art, and preventing further damage during the restoration process.
One other very interesting environmental possibility for BactoInk could be in the building of artificial corals to help regenerate damaged marine reefs. Its bone-like structure may also lend itself to biomedical applications.