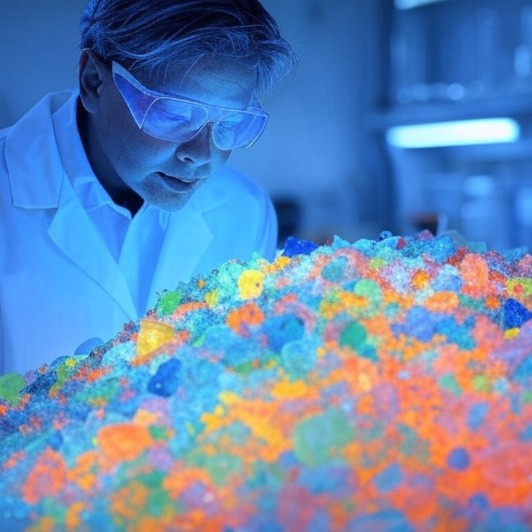
Scientists from a Swiss university have discovered a way to break down Plexiglass into its original building blocks using violet light and a common solvent, thereby making recycling plastics far more efficient and potentially helping to tackle global plastic waste.
Cracking the Plastic Code: The Science Behind the Discovery
The process, developed by lead researcher Dr Hyun Suk Wang at ETH Zurich, works by exposing Plexiglass, a type of polymethacrylate, to violet light while it is submerged in dichlorobenzene solvent. The scientists discovered that this exposure releases chlorine radicals from the solvent, which then break apart the strong carbon-carbon bonds in the plastic. The result is the recovery of methyl methacrylate (MMA), the original monomer building blocks from which Plexiglass is made.
This recovered monomer can be purified and repolymerised without losing any material quality, unlike traditional recycling methods that involve shredding, cleaning, and remelting. Those older methods degrade the properties of plastic with each cycle, whereas this new chemical process allows the material to be fully restored to its original state.
The Scale of the Plastic Waste Problem
The scale of plastic pollution globally remains a significant challenge. For example, over 400 million metric tonnes of plastic waste are produced worldwide each year and yet, only around 9 per cent of this waste is successfully recycled. Also, rather than being recycled, half ends up in landfills, while another 19 per cent is incinerated. One particularly damaging effect of our plastic use is that around 11 million metric tonnes of plastic enter the ocean annually, harming ecosystems and marine life.
Plexiglass Particularly Problematic
Polymethacrylates like Plexiglass are particularly problematic due to their durability and widespread use in industries ranging from construction to electronics. This resilience, while useful in manufacturing, makes them resistant to breaking down in traditional recycling systems.
Closing the Loop
Lead researcher Dr Hyun Suk Wang and his team have said they believe their light-based method could transform how Plexiglass and similar plastics are recycled. Dr Wang says: “By recovering monomers in near-pristine condition, we can effectively close the loop on Plexiglass production.”
The Implications
If adopted at scale, the implications of this breakthrough could include:
– Reduced use of fossil fuels. Since virgin plastic production depends on fossil resources, recycling monomers could significantly cut demand for petrochemical feedstocks.
– Lower energy consumption. The process requires less energy than current methods, which often involve high temperatures and extensive mechanical processing.
– Industrial adaptability. Preliminary tests suggest that the process can be applied on a larger scale with precision and control, making it a candidate for industrial recycling operations.
Is It Scalable?
It should be noted, however, that for this discovery to be commercially viable, several key challenges need to be addressed, which include:
– Being able to generate violet light at scale. The process depends on specific wavelengths of light, meaning industrial-level violet light sources would be necessary.
– Handling dichlorobenzene safely. The solvent used in the process is hazardous and would require strict handling protocols to ensure worker and environmental safety.
– Economic feasibility. Any new technology must be cost-competitive with the low expense of producing virgin plastics from petrochemicals.
Despite these hurdles, the researchers remain optimistic. As co-author Professor Athina Anastasaki points out, “What makes this process so promising is its ability to work on a wide range of polymethacrylates, regardless of how they were originally manufactured.”
What Next?
The research team is now working on refining the technique to handle mixed plastic waste streams, a major obstacle in current recycling systems. They are also exploring alternative, less toxic solvents to improve the process’s environmental impact.
At the same time, discussions are taking place with industrial partners to assess how this technology might be integrated into existing recycling facilities.
What Does This Mean For Your Organisation?
This breakthrough in recycling Plexiglass using violet light and a common solvent could mark a promising step forward in addressing the global plastic waste crisis. The discovery by Dr Hyun Suk Wang and his team at ETH Zurich presents a genuinely innovative approach – one that allows plastics to be broken down into their original building blocks without degrading their quality. By recovering monomers in a near-pristine state, this method could redefine what it means to “recycle” plastics, moving beyond the traditional processes that weaken materials with each cycle.
The potential environmental benefits are clear. If this technology can be successfully scaled, it could significantly reduce the dependence on fossil fuels required for producing virgin plastics, cutting both carbon emissions and petrochemical consumption. Furthermore, the process’s lower energy demands compared to conventional recycling could provide a more sustainable and economically viable solution, particularly for industries with high energy consumption rates.
For businesses, especially those in manufacturing, construction, and consumer goods, this development could offer both economic and strategic advantages. Companies that rely heavily on plastics might see reduced costs in sourcing high-quality recycled materials, avoiding the need to purchase more expensive virgin plastics. Also, integrating this technology into supply chains could help businesses meet increasingly stringent sustainability targets and regulatory demands around recycling and carbon emissions.
Beyond compliance, there is also the potential for businesses to strengthen their brand reputation by aligning with environmentally responsible practices. Early adopters of such groundbreaking recycling methods could position themselves as leaders in sustainability, attracting eco-conscious consumers and investors alike. However, industries will need to assess the commercial feasibility carefully, considering factors such as the cost of installing violet light technology and handling hazardous solvents like dichlorobenzene.
That said, significant obstacles remain. The need for scalable violet light sources and safe handling of potentially hazardous solvents are non-trivial challenges that could slow widespread adoption. Also, the economic viability of this method will need to be thoroughly tested against the low costs associated with producing virgin plastics, a factor that has historically undermined efforts to expand plastic recycling.
The optimism shown by researchers like Professor Athina Anastasaki highlights the broader potential of this technology. If successful refinements are made, particularly in handling mixed plastic waste streams and identifying safer solvents, the process could become adaptable enough for industrial-scale use.
While this innovation is not without its hurdles, this research looks as though it could open an exciting new chapter in the fight against plastic pollution. If industry stakeholders, policymakers, and scientists can work together to overcome the technical and economic barriers, this light-driven recycling method could play a pivotal role in creating a truly circular economy for plastics.